We had Linda’s homemade granola for breakfast with fresh blueberries. Berry season is just about over for the year and they will become more expensive as they have to be transported from farther away. I made a pot of Sweet Seattle Dreams, the half-caff blend that Jeff makes just for us, and we drank it in the living room. Linda checked in on the world and pulled up the latest video from NutritionFacts.org while I researched hardwood veneers on Rockler.com.
After breakfast and coffee I called Metro Environmental Services to arrange to have the culvert under the road cleaned out. They were able to schedule us for this afternoon so I accepted that appointment. I then called Brighton Honda to check on my car and left a message for Rob, the service advisor who wrote up the repair for the driver side door lock. I had no sooner left that message than I got a call from Karen at Bratcher Electric.
Mike had worked up the quote to install the 100 Amp disconnect, tie it into the output of the transfer switch, and run a 100 Amp 4-wire service entrance cable to the current sub-panel, making it into a main panel. They would also disconnect and cap the current sub-panel feed from the basement as part of the work. At just north of $1,300 it was a good $300 higher than I expected. My expectation, however, was not based on anything specific other than my own sense of the cost of materials and the amount of labor that might be involved, plus a desire for it to not cost more than $1,000.
With the phone calls taken care of we worked in the bus for the rest of the morning. Linda worked on stripping the remnants of wallpaper that remained after we removed the mirrors from the lower outside hallway wall yesterday. I worked on re-routing the heater hoses for the fan-coil heat exchangers. She got her job done before I got mine done. That’s usually the way it is.
To start, I removed one of the old 4″ round plastic grates and used my inspection mirror and a flashlight to examine the inside of the HVAC duct. What I discovered was that the two heater hoses were secured periodically with plastic cable clamps to the outer wall of the HVAC duct. I also discovered that the metal part of the duct is just the inner wall and top. The bottom is the plywood subfloor of the bus and the outer wall is the plywood wall. As originally built the metal portion of the duct could be removed but when Royale Coach did the conversion they built cabinets around the ducts and put wood wiring chases on top of them in such a way that they can no longer be removed without partially disassembling the coach.
The location of the hoses and wires in the duct was such that I could safely use my 4″ bi-metal hole saw to cut access holes for the hoses. I determined where the cable clamps were located by measuring inside the duct. I then marked where the access slots in the bottom back of the bases would be located and determined where I needed the two hoses to emerge from the duct.
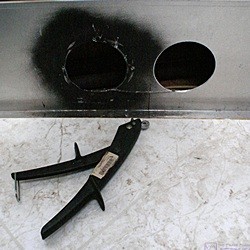
The manual sheet metal nibbler used to cut a line between the bottoms of the two holes in the HVAC duct.
There was already a 4″ hole at one of my needed locations so I drilled a second one next to it with an inch in-between. I used Chuck’s hand powered sheet metal nibbler to connect the holes together to make an opening that looked like the track around a football field. We vacuumed up the metal chips and I then installed door edge molding all the way around the edge of the opening. I was able to reach the screws holding the first pair of cable clamps with a #2SR screwdriver and remove them. This large slot will be behind the left end of the center connecting cover of the desk and the hose for the heat exchanger that goes in the left base will come out of it.
The location of the next pair of cable clamps corresponded, roughly, to where I needed the hose for the right heat exchanger to emerge. I drilled two 4″ holes, side-by-side, at that location and nibbled out the little bit of metal in-between them to make a second slot. Again, I installed the door edge molding around the entire edge. The molding was a tight fit, and I had to use a screwdriver to get it to go on the inner curves, but I got it on. The U-channel is locked in mechanically and has adhesive in it so it should stay put once it has had a few days in place. Once the hoses are re-routed I will put screen material, and perhaps some solid plates, over the openings to prevent critters from gaining access to the living area by way of the HVAC PCTS (Prevost Critter Tunnel System).
Linda had two medical appointments this afternoon, both routine diagnostic procedures, so she got cleaned up, changed her clothes, and left around 12:30 PM as I was finishing up the second slot. I went inside and was thinking about making something for lunch when the doorbell rang. It was our mail carrier, Michelle, with a package that was too big for the mailbox. A few minutes later the doorbell rang again. I figured it was Michelle again, but it was one of the guys from Metro Environmental Services. They were supposed to call first but just showed up.
I put my shoes on and walked them down to the clogged culvert that goes under the road. I was really hoping they could clean it out from the south side but when we went into the woods we could not see the end of the culvert. They got a metal detector and located the end of the pipe. It was almost completely buried and had a massive root running right in front of it from a very large nearby tree. They got a shovel and dug out around the root, exposing much of it and the end of the pipe.
The tree was probably 30″ in diameter at the base and the root was at least 10″ in diameter. I got my (new) 18″ chain saw but had trouble getting it started. It turned out it was out of gasoline. Once I got it started I tried to cut through the root on either side of the culvert. I thought I was all the way through on one end (closest to the tree) and most of the way through on the other end, but the root would not budge. I dulled the teeth on the chain to the point where the saw would no longer cut and did not want to take the time to put a new chain on just to ruin it quickly. The guys finally agreed to hydrojet the culvert from the north side of the road.
The actual cleaning out of the culvert did not take that long. The pump produces 2,000 PSI and they used about 300 gallons of water from the onboard tank on their truck. The head on the end of the hose has one forward facing nozzle and many rear/side facing nozzles. The forward facing nozzle loosens and cleans out the area directly in front of the head while the other nozzles force the head forward and blast whatever is in the pipe back out towards the entrance.
They started with a small head and ran it in until there was water coming out the other end of the culvert. They then pulled the hose back and switched to a much larger head and ran that all the way through and back. When they were done muddy water filled the culvert and the depressions on either end. On the inlet end the water was only about 3″ deep in the bottom of the culvert but on the outlet end it was near the top. They billed me for the minimum first hour amount even though I think they were here longer than that.
I called Phil to let him know what we had run into. He was surprised, to say the least, as he thought he had checked the other end of the culvert. Obviously not, but that’s water under the road, so to speak. Besides the problems with the root and the discharge end of the culvert being below the surface, it looked to me like the discharge area was something of a low spot and it was not obvious to me where water would flow from there. I have learned, however, that I am not very good at judging such things visually.
Cory, our neighbor across the street, had come over to see what was going on. He offered that the discharge area does, in fact, drain to the south through his property and eventually to Golf Club Road. Cory has been here for 30 years so I have no reason to doubt the truth of that. The elevation where Golf Club ends at Hacker and where our street ends at Hacker appears to be about the same. Our street is fairly level while Golf Club has a little bit of up and down, but it is subtle. I suggested to Phil that we might have to clear a path into the woods for his small digger and do some trenching to give the water a way out.
While Cory and I were chatting I noticed that the trees along this part of the road were hanging out over the road on both sides and were rather lower than they should be. This is the very thing I complain about with regards to the way most of our neighbor’s fail to maintain their properties along the road. I decided I should do something about it so I got our pole saw and spent a couple of hours trimming the low overhanging branches.
Linda went to the Whole Foods Market in West Bloomfield following her medical appointments and got home just as I was finishing up the pruning. She went for a walk while I called John Palmer of Palmer Energy Systems in Florida. I bought our Magnum inverter/charger for the bus from John along with various accessories and batteries. I needed a 4-wire terminal block for our Magnum Battery Monitor Kit (BMK) because I had messed up the one that came with it when I originally installed it. John confirmed that Magnum Energy had recently been acquired by Sensata, and was in the process of relocating the plant to Minnesota, but that several of the old-timers were still on board. John needed to talk to Tom anyway and asked me to call him back in a week to see if he was able to get the connector.
I checked with the service department at Brighton Honda again and Rob said he expected to get the new door lock mechanism back from the locksmith tomorrow morning and to have the car ready for me to pick up by the end of the day. It will be nice to finally have it back.
The cloudy weather finally broke today and we saw some blue sky with brighter light levels than we have had recently. The day was lovely but a little on the cool side by late afternoon so we both had a cup of hot tea. Linda took advantage of the light to work on her counted cross-stitch project, a holiday stocking for grand-daughter Madeline, and I went back to the bus to sand off the last traces of the old wallpaper from the outside wall in the hallway.
I used our Porter-Cable 1/4 sheet palm sander with 80, 120, and finally 220 grit sandpaper. The sander has an integral dust collection bag but it does not capture all of the dust. I used the vacuum cleaner to pick up as much of the residual dust as I could and then used a tack cloth to wipe down the wall.
For dinner Linda made pan-grilled tofu with caramelized onions in sweet barbecue sauce. She served it open-faced on rye bread, because that is what we had, and steamed some fresh green beans as a side dish. Yum.
After dinner I drove to Lowe’s. I needed something I could use to plug the two heater hoses to keep them from leaking as I pull them back through the HVAC duct and out through the new slots I made for them today. I ended up buying two 3/4″ barbed plastic plugs. While I was there I looked to see if they had any bleeder valves but they did not. They do not sell parts designed specifically for hydronic heating systems and I will have to go to Northwest Plumbing and Supply for such items.
While I was in the plumbing isle I looked to see if I could figure out some combination of parts to make a fill valve for the system but did not see anything that inspired me. I would love to have one or more high point expansion tanks on this system but I do not have any easily accessible places for them from which I could also run overflow drain lines. There is a good sized volume of unused space behind the drawers on the passenger side of the bedroom but it would be a very difficult place to install anything. Perhaps Northwest Plumbing and Supply will have something.
On the way home I stopped at the BP station and topped up the fuel tank in Linda’s car. I drove home with greater consideration for fuel economy than usual and managed to get the average MPG up to 56.7 before it dropped back to 55.4 as I pulled in the driveway. It will drop into the upper 40s as soon as Linda starts the engine tomorrow morning but it was fun to get it into the driveway with numbers above 55 MPG.