We were a bit sore last night, and needed a good night’s sleep, so we both took some Advil PM right before going to bed. As a result we did not wake up until almost 8 AM this morning. The Advil, combined with the very cool temperatures, made for good sleeping.
Our son had called yesterday to see if Linda could watch Madeline today while he did some work on the rental property that he and Shawna own. It was Shawna’s house before they got married, and is a nice little place, but with Madeline on the way they wanted a slightly larger place. They also wanted to be on the other side of Stadium Boulevard in the attendance area for Burns Park Elementary School and walking distance to both the school and adjacent Burns Park without having to cross any major streets.
Ann Arbor is a major rental housing market because of the University of Michigan and the local government is very involved in this market. Rental properties must be inspected at least every 30 months and meet code requirements. The rental house was scheduled for inspection on Friday and needed some minor repairs, so Brendan set aside today to take care of things. What I find interesting about this inspection requirement is that most of the rental houses our son and daughter lived in while at U of M looked to me like they had not been inspected in over a decade.
Linda was due at Brendan and Shawna’s house around 10:30 AM so she left our house at 9:15. She took the three books of wallpaper samples with her and went directly to Delux Drapery and Shades in Ann Arbor to return them and placed the order for four bolts (double roll packs) of Sellers and Josephson Just Textures Lamar paper. Not long after she left Delux I got a call at home from the store. They were looking for Linda to let her know the wallpaper was back ordered until September 11. (I’m not the least bit superstitious but September 11. Really.) To cancel the order we would have to let them know today but I told them to let it ride. I then texted Linda to let her know and she agreed with my decision.
I had a feeling this might happen and it’s what we get for waiting so long to look for, select, and finally order a wall covering. But it is what it is and we were not going to settle for something that wasn’t “right” for our interior just because it was available more quickly. If the paper actually comes in on the 11th we will have the 12th and 13th to at least install it in a few critical areas before the new seating goes in. If it doesn’t arrive by then we will deal with it when it does. Either way the only big issue is that we wanted to paper the wall behind where the desk will go before the desk is installed. As things stand we will either uninstall/reinstall the desk or paper around it.
There were several small tasks that I could have worked today but the thing that needed to be done was the installation of the pull-out pantry, so that is what I did. The pantry was already in the coach, which was a good start. I got two of the small leftover pieces of 3/4″ oak veneered plywood and set them in front of the alcove base. I then set a 5′ length of 2×4 on the flat in the space where the pantry goes and extending out beyond the alcove by more than the depth of the pantry. I then set the pantry on the 2×4, pushed it snug to the side of the alcove, and slid it towards the back of the alcove until the front was approximately one inch behind the vertical front edge of the left side panel.
There were two main reasons for using the 2×4. First, the lowest slide attached to the pantry box extends below the box so the bottom of the box needed to sit on something that was thicker than the amount by which the slide hung down. Second, a 2×4 on the flat is 1.5″ thick and that turned out to be a good thickness for positioning the pantry vertically in the alcove.
The reveal between the front of the pantry and the front edge of the alcove side panel was wider at the top than the bottom so I placed two wood shims side-by-side under the back end of the 2×4 to raise it slightly and tilt the top of the front out. I fussed with this for quite a while and each time I adjusted the shims I had to pick the pantry up, set it aside, and put it back. I eventually got the reveal to be the same along the entire length (height) of the front.
Once I knew where I wanted the pantry to be when it was closed I had to figure out how to mount the slides to the side panel of the alcove. I pondered this for quite a while. If nothing else, I have learned that when it is not clear how to proceed the best course of action is to do nothing. I have also learned that if I ponder long enough I will eventually see a way forward. Sometimes that takes days or weeks of conscious and subconscious thinking, but luckily the solution came to me relatively quickly.
The pantry box is 27″ deep. The full extension slides are 26″ deep and they are mounted so they are flush with the front of the pantry box when they are fully closed. I wanted a 1″ reveal along the front, so I needed to place the back edge of the slides 27″ back from the front edge of the alcove side panel. With the pantry box out of the alcove I used a metal ruler to measure back at three points and make very fine scratch marks. I then used the metal ruler to draw a fine pencil line through the three scratch marks.
I returned the pantry to the alcove, pushed it tight to the alcove side panel, and then pulled it out about three inches. Measuring on the back side outside the alcove I made final adjustments to the shims to get a consistent reveal. I then pulled each of the nine slides back, carefully aligned the back edge of the slide to the reference line, drilled a hole with a self-centering VIX bit, and secured it with a #6-3/4″ SR (square recessed) screw. (I was not able to initially secure the bottom slide as the 2×4 was in the way.) I pulled the pantry out a little farther until the next mounting hole in the top slide was visible and then drilled that hole on all eight slides and secured it with a screw. I proceeded in this way until all but the bottom slide were attached to the alcove side panel through every available mounting hole; 88 screws in all (11 screws for each slide x 8 slides).
To secure the bottom slide I needed to get the 2×4 out from under the pantry. I slid the pantry all the way in, slid the two pieces of 3/4″ plywood out from under the 2×4, and tried to slide the 2×4 out. Unfortunately I used a 2×4 that was too long to just slide out as part of the original pantry cabinet is directly across from the pull-out pantry. So I got my circular saw and cut about 4″ off the end of the 2×4. Close, but not quite, so I cut off another 2″ and was finally able to slide it out.
With the pantry all the way out I was able to drill and secure the mounting holes for the back half of the bottom slide. The holes for the front half were a bit tedious as I had to move the box to reveal each one. To avoid going back and forth between the drill and the screw driver bit I drilled all of the holes first and then put in the screws. I should also mention that I used the Shop Vac to vacuum up any debris that got in the slides as a result of the drilling. I also wiped the slides out (carefully, they have sharp edges) with a paper towel.
The pantry slides all the way in and out but is a little tight the closer it gets to being fully closed. I know that Jarel was very meticulous in attaching the slides to the pantry box so they were all parallel. My working hypothesis is that either I did not get them attached to the alcove exactly parallel (entirely likely) and/or there is more drag on them because of the one-sided installation (probably, but no way for me to quantify) than there would be if they were installed on both sides of a drawer.
All of the slides are on the same side, which is not how they are normally used. A pair of these slides is rated to support 100 pounds when used on both sides of a drawer, so four and a half pairs would, conservatively, support 400 to 450 pounds in a normal application. Even if they will only support 1/3 that much weight in a single-sided application that is still 133 to 150 pounds for our nine slides. I think the box weighs about 30 pounds so that leaves at least 100 pounds for stored items and I doubt that we could get 100 pounds of stuff in the pantry even if we loaded it with canned goods. Because the pantry is narrow and tall with lots of slides I suspect most of the load on the slides is vertical, which is what they are designed for, rather than sideways, which would tend to pull them apart, so I suspect that it can safely carry considerably more than 100 pounds of staples.
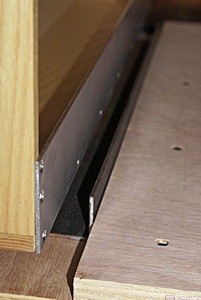
The piece of aluminum angle that will prevent the refrigerator from sliding sideways into the pantry. It is not installed yet as the plywood refrigerator base is not stained yet.
I had just finished installing the pantry and was cleaning up my tools and materials when Linda got home around 3 PM. I had skipped lunch and she had a PB&J sandwich while she was out so we agreed to have dinner at 5:30 PM. Linda picked up where she left off yesterday cleaning and waxing the drawer fronts and the woodwork in the bedroom. I decided that the oak veneered plywood base in the alcove needed to be painted or stained and then sealed so I went to Lowe’s and got a small can of Rustoleum American Walnut stain, a small can of Rustoleum satin finish polyurethane, and two foam brushes.
I brushed the stain on liberally, working in sections, let it sit for two minutes per the instructions, and then wiped it off with a lint-free cloth. The stain required mineral spirits for cleanup so I threw the brush and cloth away. The instructions said to wait one hour before applying a finish. It was 5 O’clock by then so I went to my office to check e-mail while Linda prepared dinner.
She made a nice salad and grilled a couple of vegan burgers and added some vegan cheese. Mustard, ketchup, pickles, onions, and lettuce on a nice bun made for a tasty sandwich. Two deer, a doe and her young fawn, came to our deer block while we were eating and a ruby-throated hummingbird stopped at our plants and feeders. For dessert we had half of a small, very sweet watermelon.
By the time we were done with dinner it was 6:30 PM so I went back out to the bus and applied the polyurethane. The directions said to apply it sparingly so that is what I tried to do. They also said that it could take 48 hours to be usably dry and seven days for a full cure. Drying time was dependent, however, on temperature and humidity, with higher temps and lower relative humidity promoting quicker drying.
I had run the Aqua-Hot earlier in the day and determined that there was still a little too much coolant in the system as the expansion reservoir overflowed into my catch bottle. I closed the three windows that were open, leaving them just slightly ajar, turned on the Aqua-Hot, turned on all three thermostats, and set them for about 72 degrees Fahrenheit. I will not be applying a second coat of polyurethane and cannot spare 48 hours for this one to dry.
I had thought that we might get the first sheet of underlayment installed this evening but decided we had done enough for one day. It will be the only full 4’x8′ sheet we install but it needs a notch cut out of it before it goes in. I thought it would require several cuts but then realized I had some floor leveling compound that I had not removed. I got my chisel and mini-sledgehammer and knocked off the big chunks. I then used the oscillating sander with 50 grit sandpaper to smooth everything out. It was 7:45 PM and I was done working on the bus for today.
I went to my office and spent a couple of hours dealing with e-mails. Linda was still up when I turned in at 10 PM but drifted off to sleep as I finished up this post. She has to go to the bakery tomorrow which means she will be up very early.