2014/11/17 (M) Bypass Extension
After my usual breakfast I decided to change the drinking water filter cartridge under the kitchen sink. The new one arrived UPS on Friday but I wasn’t really eager to change it, given the difficulty I have had with it in the past. As I expected, the old one did not come out exactly the way the instructions said it would and I fussed with the new one for 30 minutes without being able to get it in. Butch popped into my bus to see what I was up to and I enlisted his assistance. We fiddled with it for another 45 minutes and finally gave up and put the old one back in, although it did not go in easily. Clearly we were doing something wrong but could not figure out what it was.
I am not exactly sure what Butch and Fonda did for most of the rest of the day but whatever it was they did not need my help. I know they drained some coolant from a hose on the main engine and changed a short piece of hose. Having gotten off to a bad start with the water filter cartridge I decided to pick the coach up a bit and then work on the 12 VDC outlets for the cockpit accessories.
There’s no such thing as a “small job” on a bus conversion; there are only big jobs and really big jobs. The installation of the 12 VDC outlets involved mechanical and electrical considerations; I needed to mount them someplace that was accessible but out of the way, and I needed to be able to get 12 VDC power to that location. There is a vertical panel about five inches wide just to the right of the driver’s right leg. It runs from the floor up to the bottom of the dashboard and houses two thermometers, a cigarette lighter, and a swing out ash tray. The panel comes out after removing six screws. To the right of that panel is a house systems switch panel that was added by Royale Coach. It is about 10 inches wide and comes down from the dashboard half way to the floor. After checking to see what was behind the vertical panel I decided to mount the outlets to the passenger side of the floor-to-dash enclosure. I mounted them below the bottom of the house systems switch panel and slightly back from the front plane of the dashboard. They are very accessible in this location but tucked back out of the way enough to avoid getting kicked.
Just above the house systems switch panel is an enclosure for the CB radio. I had previously removed the four screws that secure the front panel and pulled the CB radio out of its enclosure. The power leads used spade connectors so they were easily disconnected and the incoming power harness was long enough that I was able to drop it through the speaker hole in the bottom of the radio enclosure and behind the house systems switch panel. I also disconnected the antenna coax, as it is not connected to anything on the other end, and dropped it through the speaker hole as well. I added compatible spade connectors to the wires from the 12VDC outlets including a 2-wire pigtail so I could connect both DC negative wires to the one available DC negative line. I drilled a hole for the outlet wires to go through into the space behind the vertical panel as I would eventually like to power them from there and reconnect the CB (once I get an antenna mounted). For now, however, this arrangement will do what I need it to do; power the various cockpit accessories while keeping the power cables out of from under out feet.
By 1:45 PM I had completed the installation of the outlets but I had not re-installed the various panels. I locked up the coach and the three of us got ready to go to Logansport to run various errands. Butch was wrapping up a conversation with International Thermal Research regarding the installation of his Combi unit and getting answers to a few remaining questions. It turned out that the reason the coolant circulation pump was running was that we had left the bypass switch on the Zone Control Board in the ‘ON’ position. That was also why the Summer Mode light was on. Butch turned the bypass switch off and the various indicator lights all seemed to indicate what they were supposed to show.
I ended up buying the parts for a drinking water filtration system at Home Depot. I got a GE Drinking Water Filter Housing and filter element plus a collection of hoses and fittings to connect it to the existing 3/4″” OD copper plumbing under the kitchen sink. I also picked up a can of flat black spray paint to use on the accessory mounting board for the windshield center pillar. We stopped on the way back in to Twelve Mile to pick up Daffy from the local veterinarian. Fonda had taken her there earlier and dropped her off to have her teeth cleaned. Daffy was still pretty groggy but glad to have the comfort of her owners.
When we got back to their house Fonda helped me set up some cardboard to catch any overspray and I sprayed one side and all of the edges of my center pillar board. I then headed to my coach and finished putting the dashboard panels back in. After that I turned my attention to the drinking water filtration system. It took me a couple of hours but I got the old filter head removed, mounted the new housing, and made all of the connections. I installed the new filter element and turned the water pump on, opening valves one at a time as I worked downstream looking for leaks. The only leaks I saw were small ones between the 3/8″ brass pipe nipples and the 3/8″ female pipe thread sockets in the plastic filter housing. Both leaks were easily remedied with an extra turn of the right angle shutoff valves.
I had not quite finished the water filter project when Fonda came out to let me know that Linda was on the house phone. She answered some accounting/tax questions for Butch and then we chatted for a bit. We decided that I would move the Martin Diesel appointment from this Thursday to next Monday, if possible, as the weather should be much more agreeable. That will also give me four additional days to work on bus projects here, which I need.
I returned to the coach, finished up the plumbing, made a quick dinner, cleaned up the dishes, and went in the house for the evening. Butch and Fonda had already gone to bed so I did the same and dealt with e-mails and this post.
2014/11/18 (T) Holes and LEDs
We were all busy all day today but did not have as much to show for it as we have on some other days. That’s the way it goes with bus projects. I worked on three separate projects for our bus and helped Butch and Fonda with one project on their bus.
The first thing I did after breakfast was to spray another coat of flat black paint on the oak board I plan to use as a mounting plate for various cockpit accessories. I then went to work on enlarging the return air openings above the shelf in the rear closet. This turned out to involve quite a bit of work. On the passenger side I had to cut the carpeting on the inside of the closet and peel it off. I then drilled a hole in each lower corner to allow access for a sabre saw blade. I borrowed Butch’s cordless sabre saw, so that involved getting the saw from the parts room. I cut from the back side, as I had access via the rear TV cabinet, and enlarged the opening to about 10″ x 10″.
I did not have access to the back of the panel on the driver’s side so I had to take a different approach. I removed the lower panel which gave me access to the space and the various relays mounted on the floor of the cabinet. I needed to make sure there wasn’t anything on the back side of the upper panel where I intended to drill and cut. I borrowed Butch’s lighted inspection camera, which required another trip to the parts room, and used it to look up inside. It was clear, so I cut the carpet on the inside of the closet and removed it. Working from inside the closet I did not have room to use the sabre saw, so I used my oscillating saw to cut the opening. Once the panel was cut through on both sides and the bottom it still had the metal mesh stapled to the top back side. I was able to use that to pull the mesh loose from the fixed panel and remove it.
The next step in this project will involve installing a pair of 12″ x 12″ return air grills after I vacuum up the debris from the drilling and cutting process. Home Depot carries these grills but was out of stock when we were there last night. They are supposed to be in tomorrow or Thursday. I already have a roll of 1/4″ grid hardware cloth and I plan to cover the openings with a piece of that to make sure mouse-sized critters cannot get through the slots in the grill, which will go over the hardware cloth.
By the time I got to this point it was time for a quick lunch. After my meal I checked in with Butch and he was at a point where he needed assistance attaching an aluminum angle to the driver’s side front ceiling. This angle would serve as the attachment for the vertical face of the chase that will hide the wiring running along the junction between the wall and the ceiling. With Fonda’s help we held the first piece in place and secured it with one screw near the rear end. We then measured down from the center trim of the ceiling and adjusted the other end to keep the angle as close as possible to parallel along its entire length with the ceiling centerline. With that piece mounted Butch clamped another piece of angle to the mounted one, giving us a nice straight extension of the line, and then clamped the second piece to be installed to the extension angle. I then secured the second piece to the ceiling with several screws.
Butch held 3″ Wiremold channel in place from the front air-conditioner trim to the gap between the two angles we just installed and marked it for length. Fonda cut those while Butch cut a piece of plywood to the width and length needed and then installed them. We talked about putting up the chase on the passenger side, or at least the Wiremold channel for the fluorescent ceiling lights. Butch said they planned to make that chase deeper, and I suggested they bring it out as far as possible and build it as a cabinet using a face frame with several stiles (vertical pieces) and one long, top-hinged, door. They both made note of the idea but did not want to get involved in that today.
I took a short break to call Martin Diesel and move my generator service appointment from this Thursday to next Monday. I have more to do on the bus than I can complete by Wednesday afternoon and the weather Thursday morning is forecast to still be very cold. The cold spell is supposed to finally break on Saturday with highs in the 50s and lows in the 40s. I should be able to hook up the care and leave early Monday morning in 43 degree weather; much nicer than 18 degrees (Fahrenheit).
I now turned my attention to the LED replacement lighting for the F72T12 fluorescent light fixture in the hallway cove. The first thing I needed to do was locate the 12 VDC positive and negative wires that were controlled by the pair of three-way switches; one by the pantry and the other in the bedroom. In spite of having the wiring diagram for the old fluorescent ballast on a label attached to the ballast, I was not able to trace out the wiring. Butch came over to see how I was doing so I enlisted his assistance. The situation had us both puzzled for a while but we eventually sorted it out by removing the two 3-way switches from their junction boxes and checking for voltage to chassis (DC) ground at various points. It helped that there is a second light fixture in the hallway ceiling just outside the bathroom door that is controlled by these same switches as this allowed us to know when there should or should not be voltage present at the main fixture.
With the wiring sorted out I made a short jumper wire with male spade terminals on each end and used it to jumper the red and white wires together in the base of the panty. The white wire turned out to be DC negative (ground) and the red wire ran to the far (rear) end of the chase, so this provided a ground connection at the far end of the chase. I recoded them with black tape. The other red wire at the far end of the chase was the switched +12 VDC so I now had what I needed to power the LED rope light in that space. I reinstalled the switches and cover plates and put the removable bottom shelf back in the pantry. (The old ballast and wiring is still under this removable shelf.)
The LED rope light can be cut every few inches but I decided I should test it to make sure it worked before I started cutting it into smaller pieces. I uncoiled the rope, which is supposed to be 52.5 feet long, as the instructions said not to apply power to it when it was coiled up. I attached male spade lugs to the free end of one of the power cords, made my best guess as to the polarity of the rope, attached the power cord to one end of the rope, plugged the spade lugs into the two red wires in the chase, and turned on the switch. Voila, I had guessed correctly on the polarity. I checked the full length of the rope and all of the LEDs appeared to be working. I need to check the length of the rope tomorrow to make sure it is the correct length.
The rope light came as a kit that included power cords (10), end caps (10), center connectors (10), and mounting clips (50). This should be enough material to eventually redo all four of the fluorescent cove lights and add lighting around the inside face frame of a closet or two. The lower portion of the center rear closet does not currently have any lighting and the main closet in the bathroom could certainly use more/better lighting.
I tried installing the mounting clips without much success. It was night by this time and dark enough in the hallway that I couldn’t really see what I was doing. As much as I wanted to the have this fixture functioning before I quit for the evening, I knew I had reached the end of this work for the day. Rather than frustrate myself, and perhaps mess up something, I cleaned up my tools and materials and made dinner. I had a Thai Kitchen Hot and Sour Rice Noodle Soup Bowl to which I added chopped up fresh mushrooms. It was just the thing for a chilly evening. I gathered up the day’s dishes and took them in the house to put in the dishwasher and then locked up the bus for the night. I put another coat of flat black paint on my mounting board and then turned in for the evening to work on e-mail and this post.
2014/11/19 (W) Radio Woes
I was up a little earlier than usual this morning and rather than start the day with breakfast I sprayed another coat of paint on the oak board that I plan to mount to the windshield center pillar and use as a base for various cockpit accessories. With that task completed I gathered up my cooking/eating utensils from the dishwasher and went out to my bus where I made a five cup pot of coffee and had some homemade granola for breakfast. I then got to work on the LED lights for the hallway cove.
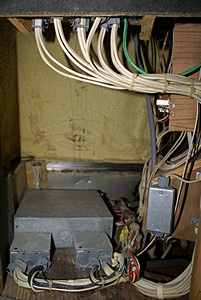
The space in the driver side rear corner of the bus. Access is difficult and it is full of wires, relays, and the bedroom a-c evaporator and blower.
I still had trouble mounting the plastic mounting brackets due to the lack of room to work but eventually figured out that I could create enough of a hole with my center-punch to get the screw started by hand. Because of the design of the chase I mounted two clips at each end and two in the middle. I started from the rear end of the chase, laid the LED rope into the mounting clips closest to the wall, brought the tube around and laid it into the other set of clips and capped the end. I inserted the two pins of the power connector/cord into the free end, turned on the power, and voilà, I once again had a functioning hallway light. I reattached the fascia board and double checked that lights still worked. They did, so I moved on to the next task.
The other three fluorescent ceiling cove light fixtures will be much more difficult to convert due to access limitations, but they are still working, at least for now, so I will leave them as is. I decided to add some of the LED rope light to the lower part of the bedroom center rear closet as it does not have any lights. (The only light is a single incandescent bulb fixture on the ceiling and the light from that is blocked by the self. Duh.) I mounted three clips inside the vertical stiles so as not to interfere with the door hinges. I cut and mounted 32″ LED rope light segments, inserted the power cord pins, and mounted the rope with the power cord at the top. An existing hole in the front corners of the shelf allowed me to pass the free end of the power cords up into the top part of the closet which has the aforementioned light fixture controlled by micro-switches on each door. I un-mounted the existing light fixture from the ceiling and identified the +/- 12VDC lines feeding it. I separated the two conductors on the free ends of each power cord and stripped them. I then cut the two wires feeding the ceiling fixture and stripped the ends. I reconnected all of the +12 wires with a wire nut and then did the same for the -12 (DC ground) wires. (This kind of work is easier to describe than it is to do, and probably takes less time.)
As long as I was working in this closet and had the access panel removed for the driver side rear corner I decided to mount the TuneTrapper FM antenna for the bedroom radio and connect it to the radio. I mounted the antenna to the ceiling just aft of the ceiling light fixture using mounting tab cable ties. I passed the coax through the a-c return air opening, down to the radio, and plugged it in. I turned the radio on but only got static and squeals. I scanned for stations but never heard one. This radio worked the last time I used it, and did not even have an antenna connected to it, so I am not sure what has happened and will need to investigate this further tomorrow.
By the time I finished all of this it was getting dark. I had complied a short shopping list throughout the day. Butch needed to go to Logansport but Bill had shown up to work on Brittiny’s car so Butch felt he had to stay home. There wasn’t much else I could do so I drove into Logansport and stopped at Home Depot, Rural King, O’Reilly’s Auto Parts, and Martin’s grocery store. Home Depot finally had two of the 12″ x 12″ return air grills I needed for the bedroom air-conditioner return air project.
While I was in Logansport I was finally able to retrieve a voice message from Gary Hatt, the publisher of Bus Conversion Magazine, and call him back. I also called Linda to see how her day went. I got a call from Butch asking me to pick up an order from O’Reilly’s. While I was there I looked at car radios but did not buy one. The situation with the bedroom radio is that it is an old two-post automotive style. They have not been made for years, having been replaced with the 1-DIN and 2-DIN form factor units, except for a couple of specialty companies that make “vintage style” radios for vintage vehicles. Because that is a very specialized market the radios command correspondingly high prices. I will modify the panel where the radio is mounted before I buy something like that.
When I got back I unloaded and stowed my groceries. I then took one of the return air grills back to the rear closet to check the fit. It was too big; way too big. I measured it and it was 14″ x 14″. Apparently the 12″ x 12″ on the label referred to the louvered area not the outside dimensions. I will be making a trip back to the Logansport Home Depot first thing tomorrow morning. I think they have a 10″ x 10″ grill which should measure 12″ x 12.” If that is the case it will fit perfectly.
When I got back to Twelve Mile I chatted with Butch and Bill for a while and then turned in for the night. I got online and registered the Ridgid drill/driver I bought last Saturday. It has a limited Lifetime Service Agreement, but only if properly registered. I then wrote this post and went to sleep.
2014/11/20 (R) Instant-Hot (Not)
My schedule has been shifting gradually since I brought the bus to Twelve Mile, Indiana at the end of September. In spite of it now getting dark by 6 PM I have been working on the bus later into the evening. This is partly due to the fact that I am working on inside projects and usually have ample artificial lighting. I did not get started checking e-mail and writing yesterday’s blog post until 11 PM and I did not turn the lights out until 2 AM. I typically get 7 hours of sleep a night, and true to my nature, I work up at 9 AM this morning. I had already planned to head to Home Depot in Logansport as soon as I got up, and by the time I was dressed I decided to skip breakfast and just go.
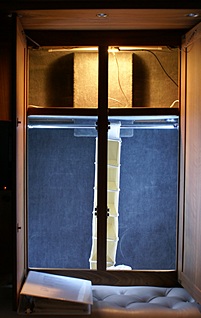
Center rear bedroom closet with LED rope lights in bottom and TuneTrapper antenna in top on ceiling.
I returned the 12″ x 12″ return air grills (that actually measured 14″ x 14″) and bought a pair of 10″ x 10″ grills (which actually measured about 12″ x 12″). It was 10:30 AM when I got back so I went across the street to Small Town Brew and got a cup of coffee rather than take the time to make my own pot and then have to clean it up later. I had a nice chat with Lisa Paul (the owner) and Harold, who appeared to be an elderly farmer but I could not tell if he was “retired.”
I took the new grills inside to the parts room to see if the square pieces of 1/4″ hardware cloth I cut and painted flat black would fit inside the lip of the grills. I had to trim about 1/4″ off of two adjacent sides on each piece. I took everything out to the bus and got the passenger side cloth/grill installed fairly easily. The driver’s side was another story. First I had to drill a hole above the top edge of the grill for the TuneTrapper FM antenna coaxial cable. The opening on this side was slightly larger than on the other side and I could not get both screws, one center top and one center bottom, to bite. I found a piece of scrap 1×1 in the warehouse and cut a 6″ length on Butch’s chop saw. I drilled two holes through it and used wood screws to secure it to the top of the opening. I was then able to screw the grill in place with the hardware cloth underneath it. I also had to work left-handed, which didn’t make the job any easier.
I vacuumed up all of the sawdust, wood splinters, and carpet fuzz from all of the cutting and drilling I had done in this area in the last few days. The grills are white but I decided not to paint them as they are inside a closet. I installed them with the louvers facing the rear of the closet so when the doors are open you cannot see through them into the space behind. They look OK and, more importantly, will allow unrestricted airflow into the squirrel cage blower on the bedroom air-conditioner evaporator.
As long as I was working in the rear closet I coiled and secured the extra length of FM antenna coax. I then located the speaker wires for the radio. There were wires for four speakers, which I presumed were the two in the bottom of the overhead cabinet in the bedroom and the two under the wall cabinet in the bathroom. All of the power wires were also part of that harness. I was not able to determine why the speakers quite working, so I disconnected all of the wires from the radio, removed the knobs, retaining nuts, and faceplate, and took it out of the panel from the rear. There are a LOT of wires behind this panel and it was not easy to get the radio out. (The radio is mounted in a panel next to an alarm clock and under a row of pushbuttom switches. This panel is installed under the main 240/120 VAC house electrical distribution panel, above which is the evaporator/blower portion of the bedroom air-conditioner. That’s a lot of stuff with a lot of wires in a place that is difficult to access; another brilliant Royale Coach conversion feature.)
The evaporator is installed with the coils not centered in the opening. In particular there is a 1″ gap along the bottom edge and a similar opening along the top edge. The problem with this is that it provides a very direct path for air coming out of the unit to be drawn back in rather than coming from the return air grill. I purchased two different sizes of foam weather seal at Rural King intended for sealing around the edges of a window mounted air-conditioner. I cut appropriate lengths of this material and secured it in place using double-sided tape I got from Fonda.
I decided to mount the indoor/outdoor thermometer on the wall between the refrigerator and the house systems panel. It only needed one small screw and a small piece of double sided tape towards the bottom to hold it to the wall. It’s a nice location and should give a more representative temperature reading, being on an interior wall at eye level and not in direct sunlight or near the kitchen counter where the cooking gets done. It’s also next to the refrigerator so it should have a strong signal from the outdoor remote sensor, which we keep on the middle shelf of the refrigerator compartment. As long as I was fiddling with this, I changed the batteries on the remote sensor and the base unit.
I checked in with Butch and Fonda to see if they needed my help. They were also working on inside projects, both bus and house, and did not need my assistance today. If they do need my help they know where to find me and are not bashful about asking, but I still like to check in with them several times a day.
My next task was to remove the Insta-Hot water heater from the kitchen sink. It has never worked since we got the bus, which is to say no water comes out of it when I depress the lever. I also have no idea if the electric heating element still worked as we have had it unplugged. I shut of the water pump and closed the primary cold water inlet valve and both the inlet and outlet valves on the new water filter. I loosened the 3/8″ tube compression nut on the supply line and pulled it loose from the supply T. I purchased two 3/8″ compression caps yesterday at Home Depot. I applied Teflon tape to the threads on the T, screwed a compression cap on, and tightened it. I re-pressurized the line, checked for leaks, and found some. I tightened the cap more but I could not get the leaks to stop.
I again shut the pump off, closed all of the relevant valves, and opened the filtered drinking water faucet to relieve the pressure. I borrowed Butch’s Teflon pipe thread sealant, cleaned the Teflon off the threads on the T, applied the sealant, and screwed the second cap on. I tightened the cap and re-pressurized the system. It leaked worse than before. I tried to tighten the cap more and the leak got worse. It was time for plan B.
The hose coming out of the new water filter feeds a T from which a line went to the Insta-Hot. The other end of the T is connected via 3/8″ tube to a second T. One line from that T supplies the drinking water faucet. The end of the second T feeds the line for the ice-maker in the refrigerator, which we have valved off behind the fridge and unplugged. The first T was no longer necessary and the second T wasn’t really either. Given that I could not cap the first T successfully I decided to remove it. That left the second T with a short length of 3/8″ tube with a compression sleeve and nut already in place. The hose coming off the output side of the new filter housing was long enough to reach to the second T. I snugged up the compression nut and restored pressure to the system. No leaks! Hurray.
My final project for today was wiring up a 120VAC outlet in the bathroom closet for the InterVac built-in vacuum cleaner. The vacuum cleaner is installed in the hallway wall just to the left of the refrigerator and below the house systems panel. The bathroom closet is on the opposite side of that same wall. The closet has a false bottom with a removable panel that provides access to a 6″ deep space full of wires, hoses, and heaters. Of particular interest to me was the Cadet electric toe-kick heater which runs on 120 VAC (~10 Amps) and is on its own circuit breaker.
I removed the access panel and then removed the thermostat knob and the front cover/grill (two screws) from the toe-kick heater. I removed two more screws and the heater slid out the front of the toe-kick board. I removed four small screws, took the top cover off, disconnected the power wires, and pulled them out the back of the unit. I got a surface mount duplex outlet and a square metal junction box (with cover plate) from Butch. I drilled a hole through the bottom of the closet next to the rear wall that was tucked under the shelves to the right. I cut a two foot length of 14-2+g NM cable and used it to wire up the surface mount outlet. I fed the wire down through the hole, and screwed the outlet to the rear wall. I installed a strain relief in the back of the Cadet enclosure, cut a two foot length of 12-2+g NM cable, routed it into the Cadet, and completed the AC power connections. I then put the top cover back on, slid the unit back into the recessed toe-kick, secured it in place, and put the cover/knob back on. I routed the original power cable and the two new cables into the metal junction box, made all of the electrical connections, and put the cover plate back on. I put the cover on the new outlet and plugged in the InterVac power cord, which comes out of a grommeted hole in the back wall of the closet. I turned the circuit breaker on, turned the heater thermostat up, and it came to life. I turned the thermostat back down to shut the unit off and turned the vacuum cleaner on. It worked too. I put the access panel back in place, gathered up all of my tools and supplies, and then swept up all of the construction debris.
The refrigerator has been running a bit colder than I would like so I made small adjustments throughout the day. The unit was suddenly running at 44 degrees instead of the 35-37 degrees it had been indicating. I removed the thermometer base unit from the wall and set it up in the refrigerator next to the remote sensor. I will check it in the morning and see if they are in agreement.
Linda called around 8:30 PM and Butch came out to let me know. We chatted briefly and I went back out to the coach to finish up and have a light dinner salad. I wrapped up at 10 PM, locked up the bus, and went into the house. Butch and Fonda had already turned in for the night. Their oldest daughter, Gene, is getting married tomorrow in Indianapolis and they would be leaving early in the morning.
2014/11/21 (F) Wedding Bells
I set my alarm for 8 AM to make sure I was up and dressed before Butch and Fonda had to leave. Gene, the older of their two daughters, was getting married at 4 PM today in Indianapolis and there were a few details I had to go over with Butch and Fonda before they left. They were still getting ready so I went across the street to Small Town Brew to have a cup of coffee and chat with the proprietor, Lisa Paul.
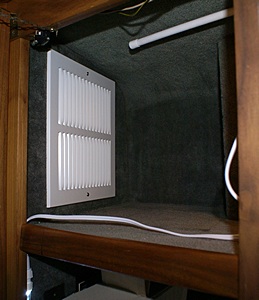
The first of two return air grills that allow air to pass through the upper portion of the center rear closet. The TuneTrapper FM antenna is visible upper right.
When I returned to the house Fonda showed me how to operate their washer and dryer and the various additives she uses. She pre-measured the food for the dogs and told me what time to feed them, when they needed to be taken outside, and the policy on “cookies” (dog biscuits). Butch gave me a house key so I could come and go as needed. He found some audio speakers that might be useful in diagnosing the problem with the bedroom radio. He also found a multi-probe digital thermometer that I could use to check the temperatures of the bus refrigerator and freezer compartments and ambient room temperatures against the Indoor/Outdoor thermometer we use for that purpose. They loaded up the car at 9:30 AM and left to pick up Bill Tharpe in Mexico (Indiana). Bill was flying out of Indianapolis to meet a friend in Arkansas (state of) and drive her back to Indiana and the timing was such that he could catch a ride down to the airport with them.
As soon as they left I sorted my laundry into lights and darks and loaded the lights into the washing machine. I used my own detergent, which is free of dyes and perfumes, as years ago I had a bad reaction (contact dermatitis) to a name brand liquid laundry detergent. With the laundry started I took the digital thermometer to my bus and had breakfast. I read the directions for the thermometer, plugged in the probes, and turned it on only to discover that the 9V battery was low (depleted) and needed to be replaced before I could use the instrument. It was a cool but sunny day!—a nice day for a drive—so I locked up the bus, transferred the laundry from the washer to the dryer, locked the house, and headed to Walmart in Logansport.
I was back in an hour, by which time the dogs needed to be taken outside. With that chore done I put the second load of laundry in the washer and restarted the dryer on the driest setting. I put the new 9V battery in the digital thermometer, plugged in the three probes, and turned it on. I put one probe in the freezer, left one buy the counter (for ambient air temp) and put one in the fridge next to the base station and the remote sensor. The digital thermometer is accurate to 1/10th of a degree Fahrenheit. It is a serious piece of test equipment that Butch used for professional HVAC work, so I regard the temperature readings as correct compared to our indoor/outdoor consumer unit. For the rest of the day I kept a log of the time and temperatures each time the refrigerator compressor started and stopped.
After studying the manual for the bedroom radio, a Kenwood KRC 3004, I worked for a while on the bedroom control panel where it was mounted. After struggling with getting the radio out yesterday I realized today that the wood bezel surrounding the panel was removable, allowing the whole panel to come out and providing easier access to its back side and the wiring behind it. That did not change my opinion about the design of this aspect of the bus conversion; it simply was not done with the idea that it would ever have to be worked on.
I had disconnected the harness for the four speakers powered by this radio yesterday so I checked at the connector for proper resistance and shorts. Each speaker measured around 4 ohms (DC) and none of the negative lines were shorted. (Technically the 4 ohm rating on a speaker is an AC impedance, not a DC resistance, but the resistance reading told me there was a complete circuit from the connector through the two wires and the speaker coil.) The power supply wires appeared to be in tact so I reconnected the radio and turned it on. I heard some static and could “move” it from the bedroom to the bathroom with the front-rear fader control but as soon as I tried to turn the volume up the speakers went dead.
This was starting to sound like a volume control component problem so I removed the top cover of the radio. The volume control was a component about 1/2″ square and 3″ long mounted to a vertical circuit board on the left edge of the chassis. There wasn’t much I could do with that but tomorrow I may spray it with some De-Ox-it just for grins and giggles.
I interrupted my work around 4 PM to feed the dogs and take them outside. I was thinking about what to work on next and remembered that the latch side stile of the left closet door in the bathroom was coming loose and was difficult to latch. I needed two “L” brackets to reinforce the upper and lower corners on the inside of the door where the stile connected to the top and bottom rails. For the second time today I locked the bus and the house and headed to Logansport. This time my destination was Home Depot, but it’s adjacent to the Walmart so it was still the east end of town. I also went to Radio Shack, in McCord’s Do It Best Hardware, looking for a replacement radio but they do not sell car radios anymore.
I called Linda while I was in town and described the work I was doing. She sent me a TXT message with data on our refrigerator at home. Over the course of an hour the compressor cycled 7 minutes on, 13 minutes off. That was useful information. That’s a duty cycle of about 1/3 or 33%. Our bus fridge duty cycle was ~60% (30 minutes ON, 20 minutes OFF). I think our home fridge is more like what I would expect, but I will discuss this with Butch. What bothers me the most is how long the bus fridge runs when it comes on; 4x as long as the house fridge.
By the time I got back it was dinnertime. I heated a Tofurkey Italian sausage with some diced onion and used it as a topping for a plate of salad greens, along with some roasted peanuts and raspberry walnut vinaigrette dressing. I then worked on the bathroom closet door while I continued to monitor and record the refrigerator and freezer temperatures. I also repositioned the ball catches on the door so it now closes easily and latches securely.
I was watching the data from the digital thermometers and happened to be looking at the readings from the one in the freezer when the cycle ended. The temperature was around 0 degrees F and as soon as the compressor stopped running I watched the temperature climb 1/10th of a degree every few seconds. The compressor seemed to come back on when the freezer reached a temperature of 10-to-12 degrees F. If I presume a 10 degree rise (to keep the math easy) and the off time is 20 minutes, the freezer is heating up 1 degree F every 2 minutes (120 seconds). That’s 1/10th of a degree every 12 seconds, which seemed pretty fast to me. I also noticed, however, that the temperature in the refrigerator compartment continued to drop a few tenths of a degree after the compressor stopped, so perhaps that’s where the cold from the freezer was going.
How a refrigerator cycles depends on a number of factors: the efficiency of the unit, the ambient temperature, where the controls are set, how much and what kind of stuff is in the freezer and fridge compartments, and how often the doors are opened and for how long. I don’t have any food in the bus freezer but there is plenty of mass in the form of containers of frozen water. I don’t have much food in the bus fridge compartment either, but I have a lot of bottled water, “milk”, O. J., salad dressings, mustard, etc. and I have it distributed from top to bottom, including the door shelves. I have the thermometers on the second shelf from the top.
I had spent quite a bit of time earlier taking voltage measurements on the push-button switches in the bedroom control panel in an attempt to figure out why the aisle lights were not working. I was fairly certain this was a 3-way circuit with a second switch. I found the “other” switch by the dinette, changed its position, and voila, the aisle lights worked! For some reason that switch, the rearmost switch by the fake plant, appeared to not be wired as a 3-way with the one in the bedroom but rather to be in series with it; both switches have to be on for the lights to work. That may not be how they are wired, as there could be a relay involved, but that’s how they behave.
I wrapped up my work for the day at 8 PM, locked up the bus and went in the house. I took the dogs out and then gave them each a treat. I folded and packed my clothes and then settled in to write while I waited for Butch and Fonda to get home. They arrived at 10 PM and we chatted for a while about the wedding/reception, refrigerators, and radios before finally turning in for the night at 11 PM.
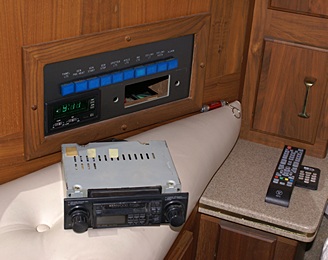
Bus bedroom driver side rear corner house systems control panel with Kenwood KRC 3004 radio removed.
2014/11/22(S) T Minus 2
…and counting. Today was my second to last day to work on the bus in Twelve Mile, Indiana. Except for a few days in October, the first full week of November, and some weekends, I have been at Butch and Fonda’s place since I brought the coach here on September 30. We have gotten a lot done on both buses in that time, but not everything on either list. As much as I wanted to avoid a last minute scramble, there was still too much to do to take the weekend off. I was up at 7 AM, took a shower, got dressed, finished yesterday’s blog post, and got to work. I stayed busy until 10 PM, with short breaks to have a bite to eat and one trip to Logansport late in the afternoon.
My major accomplishment today was mounting the oak board to the center windshield pillar and then mounting the magnetic compass and Pressure Pro TPMS receiver to it. I needed a standoff to mount the inclinometer, so I cut two pieces of 1×1 and spray painted them flat black. I will finish mounting the inclinometer tomorrow, and possibly the inside rearview mirror.
My other major project was the removal, disassembly, diagnosis, repair, testing, and reassembly of the driver’s side motorized windshield roller shade. Fonda helped me remove it and Butch helped with the rest of the process. It appears that the problem was a soldered connection to the internal motor that failed. I will reinstall it tomorrow, probably with Fonda’s help, and try to correct some alignment problems in the process.
I sprayed the on/off/volume control in the Kenwood KRC-3004 radio with De-Ox-It and left it to dry. I came back later, plugged the connector into the back of the radio, and turned it on. Nothing, nada, zip; zero sound from the speakers. I suspect the volume control or the final output transistors have failed. Either way I am not likely to get it repaired. While I tend to think of Kenwood as good equipment, both of the radios in the bus have something wrong with them. The front radio is obviously newer as it has a 1-Din form factor. This will also make it easier to replace when I get around to it.
The bedroom radio is an old style unit with two shafts that are used to mount it and control most of the functions plus a center section for the cassette player, LCD display, and a few buttons. This style of radio is now considered “vintage.” There are at least two companies that make modern radios in authentic vintage form factors, but they are very pricey and targeted at the vintage restoration market. Putting a modern 1-Din form factor radio in the bedroom panel will require me to cut the appropriate size opening. Since the panel has 10 switches mounted in it creating the opening will be non-trivial. A better option would be a remote radio with a slim profile control head, like the one Butch has from Custom Autosound. The control head would cover the center opening and I could mount switches in the two shaft holes. I thought of that riding to Logansport. Our trips to town are often useful that way.
Another thing I did today was continue to monitor and adjust the refrigerator. Since I spent much of the day working in the bus I was able to log the time of day and various temperatures each time the compressor started and stopped. I missed cycles, of course, as I was in and out of the house or gone to town, but I think I got enough data to determine if there is a consistent difference between the indoor/outdoor sensors and the more accurate Cooper Instruments SH66A digital thermometer, and if so, how much and in what direction. I also have useful information about the settings of the refrigerator (thermostat) control and freezer (air control) for the temperatures I want to maintain in the two compartments. I will continue to monitor tomorrow as I wrap up my last few tasks and organize the bus for travel. I entered the raw time and temperature data into an Excel Spreadsheet but did not have time to analyze it. Big day tomorrow; have to get to bed.
2014/11/23 (N) T Minus 1
Today was my final day working on buses in Twelve Mile, at least until we return here a week from today. The temperature continued to be mild but by noon it was raining. I had breakfast and got to work as I had a long list of little things to take care of today.
I continued to monitor the refrigerator/freezer temperatures and record them while working on other projects. I taped a piece of cardboard to the back of the bedroom control panel to cover the holes where the radio used to be and reinstalled the panel. I reinstalled the driver side access panel in the lower rear closet and then vacuumed up the sawdust and other construction detritus. I started organizing the inside of the coach for travel, getting things in boxes and getting the boxes on the floor on the two front sofas. Twelve Mile now has a large recycling container that accepts mixed recyclables, so I carried several bags of plastic, cardboard, and cans over there rather than haul them back to the house.
Steve showed up mid-morning and helped Butch install a new AM/FM radio and CD player in the MC-9. They also came over and helped me reinstall the driver side windshield roller shade. We tested it and it worked. I like it when that happens. I wasn’t as lucky with my mounting arrangement for the inclinometer. I ended up modifying one of the pieces and then had to repaint the two ends flat black. I left it to dry and busied myself with getting the bus ready to go to Gallahan’s Truck Stop for fuel. I had turned the electric block heater on earlier so I turned it off and turned on the Aqua-Hot engine preheat pump.
I used Butch’s portable air compressor to air up the chassis (suspension, brakes, and engine accessories) and used his auto shop compressor to adjust the inflation pressures of the tires. I have the 12VDC accessory outlets in the cockpit powered off of the house batteries, so I immediately checked the Pressure Pro TPMS sensor readings against the known pressures in the tires. The correspondence was as follows (actual:sensor): DSF (116:112), PSF (116:111), DSOD (95:92), DSID (95:91), PSOD (95:91), PSID (95:91), DST (85:83), PST (85:83). All of the sensors are reading low from 2 to 5 PSI. I need to create a little card to go by the display unit with these calibration adjustments.
Butch had to take Steve to Rochester to meet up with his wife and I was just getting ready to lock up the buildings so I could drive the bus to Gallahan’s when Fonda returned from church. I stowed the folding step stool in the back of the car, unplugged the electrical shoreline and stored it just inside the warehouse overhead door, disconnected the portable air-compressor and stored it in the parts room, and turned off the Aqua-Hot (anything with an open flame is a no-no at a fueling station). I fired up the engine and was about to leave at 1 PM when Butch returned.
I drove to Gallahan’s in light rain. The new speedometer/odometer worked as intended, and I did not get a Check Engine Light (CEL) during the trip out and back. I discovered, however, that my transmission retarder was not engaging. I suspect that has something to do with removing and reinserting the cable connectors on the DDEC II when I was trying to diagnose and fix the Fuel Temperature Sensor Voltage High code problem. Not having the transmission retarder is not a good thing, but there wasn’t anything I could do about it today. I will probably try to figure this out on Monday, December 1st while we are parked back at Butch and Fonda’s awaiting our group departure for the southwest U. S.
When I got back from Gallahan’s I pulled the bus in front of the automotive garage so I could pull the car up behind it. A lake was forming behind the bus, so I pulled up farther. Butch has a 30 A RV outlet on the front of the garage, which was plenty of power for the unoccupied bus. I moved all of the stuff I had stored in the parts room to the overhead door for the woodshop, which is directly behind where I normally park the bus. I backed the car up to the door close enough that I could open the rear hatch and load everything into the back of the car while staying out of the rain. I packed up clothing I was not going to need and loaded that in the back as well.
Once the car was loaded I pulled it around behind the bus and hooked it up for towing. By this time there was a hard, steady, rain but I just worked through it. All of the lights tested as good and the bus/car combination was ready to roll tomorrow morning. I turned on the Aqua-Hot and turned up the heat while I prepared a couple of tofu hotdogs for a late lunch / early dinner.
I re-mounted the inside rearview mirror high enough that I will not bump my head on it like I used to. I retrieved the mounting part I had spray painted earlier and tried to finish the installation of the inclinometer, but could not get it to work. I will either have to take the case apart to get the mounting bracket loose or I will have to rethink/re-engineer how I mount it. That was my last project. I would rather not have ended on a note of failure, but it meant I have at least one project to look forward to. I gathered up a few cooking/eating utensils, my camera, and a notepad, shut off the lights, and locked the door on the way out.
Back in the house I took a hot shower and put on some dry clothes. I loaded all of the wet/soiled clothes in the washer and Fonda did a small load of laundry for me, transferring it to the dryer as well. The three of us chatted while they ate dinner. Linda called at 8:30 PM and we discussed the weather forecast for tomorrow, which, while well above freezing (to start) was less than ideal with rain and high wind advisories. I decided to try for an earlier start than I originally planned. With any luck I can be at Martin Diesel by 9:30 AM and on the road for home by 2 PM. That would get me back to the house while it’s still daylight.