[ There are 3 photos for this post. ]
As November gave way to December, it became clear that we had reached the stage in this project where sayings such as “the last 10% of a project takes 50% of the time” always seem to come into play. Not labor hours, of course, but calendar time, and visible milestones, for sure. The building is constructed; the electrical service entrance (meter enclosure, main panel, and outlet/receptacle) is installed, inspected, and approved; and the driveway is finished (for now). Separate from the building contract, the 2” Schedule 40 PVC electrical conduit has been trenched in from the meter enclosure to near the existing utility pole. Other than wiring the building, which is on me to do, it looks/feels like we are very near completion of the builder’s portion of the project, but big things remain to be done.
FRIDAY 02 December
Chuck, the builder, let me know that he had finally gotten an estimated availability date from the vendor for the two large roll-up doors … December 28th (of this year). There is always a list of a few minor things that need to be done or corrected, but these doors are one of the two remaining major components of the actual building construction, the other being the gutters. At this point, I presumed that they would not be installed until early in the New Year. Work on this project started in the second half of June, not long after we left for our 4-month journey through Eastern/Atlantic Canada, so mid-January would mark the seven (7) months point.
TUESDAY 06 December
Today was a big day; we finally received the costs to have the electric power on our property upgraded and extended to the new accessory building (RV barn, workshop, storeroom). Also, sometime today (or yesterday) the gutter sub-contractor was apparently here and installed the gutters and downspouts on the two long sides of the barn.
WEDNESDAY 07 December
Today was, perhaps, an even bigger day than yesterday, as I finally received the actual contract for the electric utility work. All that remained to do was read it carefully, sign it, scan the pages, and e-mail them back to a special e-mail address at DTE Energy. I looked the contract over, especially the costs. The language used throughout the documents was specialized for DTE’s purposes, but I had a sense of what was what, and everything appeared to be in order. I was missing a diagram that the cover letter said I was supposed to have, and had a few other procedural questions, so I e-mailed our DTE planning consultant back.
The most expeditious way to move things along was to scan the signed documents and e-mail them back. This would trigger a reply e-mail with a link to a special payment website. I decided to hold off submitting everything until tomorrow so I could read all of the boilerplate contract language.
The way the project was now moving, and with real winter just around the corner, it appeared that I might not get any wiring done in the barn until spring. Since I would have time between now and then, I had been considering purchasing the 2023 version of the NFPA 70 / NEC (National Electric Code) Handbook, which will be available on December 15, 2022. It’s a bit spendy, but the Handbook contains the complete text of the CODE along with extensive inline commentary, diagrams, and photos that “explain/illustrate” what the CODE language means, and how it is applied in practice. That sounded like some interesting and meaningful “home study” over the early winter months.
The builder was here today to see what was wrong with the shop and storeroom doors, and fix them if possible. Before looking at the doors, we were both surprised to see that the gutters had been installed (on the long sides of the building).
Both doors are very difficult to open, and both of them have dead-bolts that will not slip into their strike plates, even with jiggy-jogging them. Chuck determined that the difficulty in opening was due to bottom sweeps that were a bit too thick, although they might become a bit more compliant with use and age. The sweeps snap in and out fairly easily, and he will try to get slightly thinner replacements for both of them.
The storeroom door appeared to be installed correctly, with an even reveal between the door and the frame on the inside and with everything square. The solution for the dead-bolt will be to grind the strike plate, which is OK with me. (It’s what I would have done if I was fixing it.) He would have to come back to do that.
The Shop door, however, was not installed correctly, being slightly out of square and not having an even reveal between the door and the frame from the inside. Chuck said he would be out in the next few days to remove it and reinstall it, or have one of his carpenters do it. It’s already trimmed out, so I don’t know if that means removing and reinstalling all of the trim, but he said it was the only correct way to fix the problem.
THURSDAY 08 December
Linda had to go into the bakery today, so during the first part of the morning I read over the entire DTE contract package. I then signed it in the two places that I needed to, and scanned those two sheets, saving them as PDFs and renaming them for clarity of content. One was the “Line Extension Agreement” and the other was the “Secondary Services Agreement.” I attached both PDFs to an e-mail and provided additional contact information per the information from my DTE planning consultant, and sent the e-mail off to the special DTE e-mail address. I wasn’t sure how long it would take for DTE to respond, so I left to run some errands.
While I was out, I got a text message with the payment link. So far, so good. When I got home, I also had an e-mail with the payment amount. But I had a second e-mail indicating that I had not submitted all of the required documentation. I spent the second half of the afternoon scanning the rest of the pages into PDFs, renaming them, attaching them to an e-mail (along with some additional information), and sending it off to the special DTE e-mail address. By then, it was late enough in the day that I was tired of dealing with this and ready to sit on the sofa and work a puzzle or watch a Youtube video while I waited for Linda to get home.
After an easy dinner of salad and pizza, Linda used the payment link and paid the invoice. Correct documents or not, they were more than happy to accept our money (CC).
I will check e-mail tomorrow morning to see if I got it right on the 2nd try.
FRIDAY 09 December – WEDNESDAY 14 December
Well, the contract was accepted as complete and we received verification that our payment had been received. I contacted our DTE planning consultant to let him know. He replied back that it might take a couple of days for him to receive official/internal confirmation, at which point he would generate the work orders needed for the project. That internal communication eventually took place, at which point I was notified that the work would “probably” be completed by the end of January, but not later than 17 February (2023). That was discouraging to hear, but this was the first time I had dealt with DTE on a project like this, so I was not familiar with all of the steps or the timelines involved. Regardless, it was out of my control.
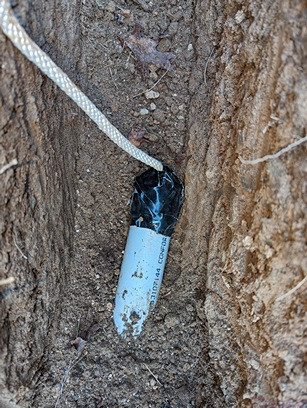
The free end of the conduit near the utility pole with the 7/16″ rope passed through the hole in the end cap and everything taped to prevent dirt and water intrusion.
Sometime prior to the 14th, the DTE planning consultant made another site visit to have a second look at the utility pole replacement and the conduit we had installed from the pole to the barn. Because the conduit runs downhill from the pole location to the meter location, he suggested I try to seal up the open end by the conduit as best I could to prevent water/dirt from getting in. Given the time of year, if water got into the conduit and froze it would prevent the cables from being pulled through and we would have to wait until the spring thaw to get the service conductors installed from the pole to the barn. He also marked the location for the ground pedestal (junction box), but indicated that the crew(s) that did the work might place it in a slightly different location.
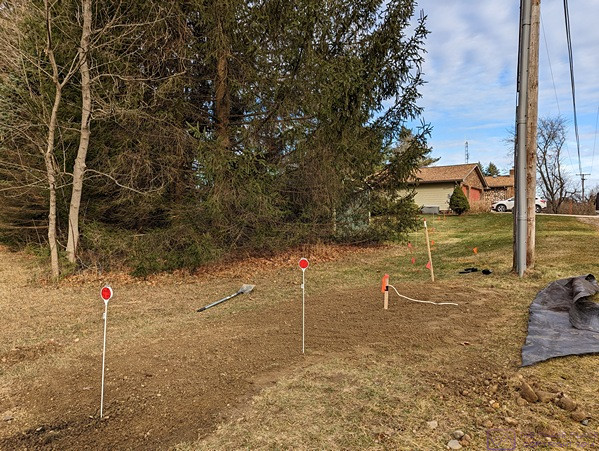
A view of part of the trench, filled in and raked out.
Marty and I had placed a 7/16” rope in the conduit after we assembled it and put it in the trench. One end was tied around the lugs in the meter can, and the other end came out the open end of the conduit and up a wooden stake marking the end of the conduit, as we planned to bury it, where it was tied at the top so the end could be easily located later. I had tried to seal the open end with a rag, but this was not adequate. I had a cap with a domed end, so I drilled a 1/2” hole in the end of it, fed the rope through the hole, and slid the cap over the end of the conduit. Although not glued, it was a snug fit. I taped around the rope at the hole, and around the cap and conduit with Gorilla tape. I retired the rope to the wooden stake, and then buried everything.
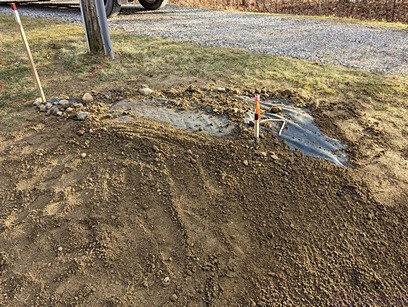
The trench beyond the free end of the conduit has been back filled and marked with a stake that secures the rope. Plywood has been put down and covered with plastic and dirt to keep as much water out as possible.
THURSDAY 15 December – SATURDAY 31 December
With the holidays coming, and a trip planned between Christmas and early January, not much else happened on this project the rest of the month. The builder was notified that the roll-up doors were now delayed until the end of January, 2023. Oh well. Again; out of our (and his) control.
…